

Why did Smeding choose us as a partner?
- Our previous experience with similar projects in the Food & Agriculture sector was one of the decisive factors.
- Our expertise with working with batches and detailed batch registration in the fresh produce industry, as well as our experience with the applicable laws and regulations and traceability, was also a decisive factor.
- Our knowledge and experience with SAP and our approach to similar large implementation projects were important in Smeding’s decision.

'We have control over our scheduling, enabling us to provide perfect customer service'
More than 6,000 orders a day, often with same-day delivery. 1,800 products in their product range, 25,000 m2 of warehouse space and 25,000 customers. Add to this immense operation a service where, as a food retailer or food service company, you can still place an order until late in the evening, including the option of partial deliveries, and you will understand that order and warehouse scheduling is quite a challenge for Smeding Groenten en Fruit. Through the implementation of SAP S/4HANA, the company added efficiency and gained control over these crucial processes within its organisation. And that is essential if you wish to grow within a dynamic market and distinguish yourself from the competition. In this case study, we explain exactly how we achieved this and how it has benefitted Smeding to date.
About Smeding Groenten en Fruit:
Industry: Food & Agriculture
Products: Procurement, sales and logistics of fresh potatoes, vegetables and fruit for the food retail and food service industries throughout the Netherlands and Belgium
Locations: Sint Annaparochie (headquarters and distribution centre) & Breda (distribution centre)
Employees: 500+ employees
Website: smeding.nl
Challenges and advantages
What challenges did Smeding face before implementation?
- The legacy system in use was no longer sufficient and an upgrade was too risky.
- No proper integration between warehouse systems and processes such as sales and order processing, which compromised order fulfillment and delivery reliability.
- Data sharing between departments was also hampered.
- There was no direct insight into inventory, while stock levels were different every hour due to the high throughput rate.
- Achieving hourly planning and proper stock distribution among customers was difficult with the old system.
- As the fresh produce and food market is unpredictable, Smeding wanted more flexibility in terms of its scheduling and delivery activities.
- Too little control over packaging flows.
What improvements has Smeding seen?
- All business processes – from procurement to sales and logistics – have been integrated. Everyone uses the same data, which enables a clear picture to be formed in real-time of the current situation.
- Operational efficiency has grown. Fresh products can now be ordered, collected, and delivered at a detailed level all day long. The IT, business processes and layout in the warehouses have been harmonised for this purpose.
- It is possible to plan by the hour, which significantly increases delivery reliability and service to customers.
- Thanks to the product distribution tool in the system, stock items are better distributed among customers, reducing the number of non-deliveries. In this way, Smeding increases customer satisfaction. The tool also suggests alternatives.
- Packaging flow management has been optimised, giving Smeding a better insight into packaging balances at supply chain partners.
Which solutions have we implemented?
- SAP S/4HANA – on-premise hosting– with industry-specific modifications for Smeding’s unique business
- SAP Extended Warehouse Management – advanced
- SAP Transportation Management
- MAKIRA (master data management)
- GLASSWING (document handling)
More customer cases


SVZ, frontrunner in the food industry for more than 150 years, strives to offer highest quality in production and supply of purees, juices, and concentrates made from freshly picked fruits and vegetables.

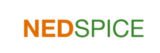
To strengthen their ambitions, the company wants to capture sustainability throughout the chain. Thanks to SAP S/4HANA and our it.agriculture accelerator, we made a fully traceable supply chain possible.


We transformed a local ERP system into a single solution that consolidates the data of all their international branches. Read how we helped BIP in their digital transformation.